Advancing battery technology is fundamental to promoting the adoption of electric vehicles (EVs). Batteries are an integral component of EVs and have a direct impact on variables such as driving range, charging time, cost, and overall performance. However, without further advances in EV battery technologies, such as new battery materials and designs, EVs will not reach their full potential.
This article outlines how EV batteries have evolved, key challenges in EV battery R&D moving forward, and the role of battery simulation in EV battery R&D. It also highlights battery simulators from REGATRON AG, an internationally recognized Swiss company renowned for quality, accuracy and creativity in the field of power supplies.
Battery modeling and battery simulation:
Battery modeling and battery simulation are two increasingly important approaches in EV battery R&D. Though closely related, they play different roles in understanding and analyzing battery behavior.
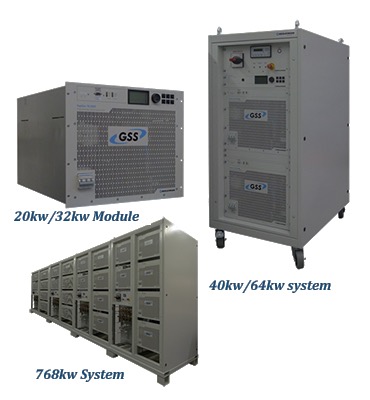
Battery simulation modules/systems from REGATRON
Battery modeling generates mathematical or computational representations of a battery system and provides a theoretical explanation of its electrochemical, thermal, and electrical characteristics. It outlines the behavior of a battery through equations and mathematical relationships.
Battery simulation applies a battery model to predict or emulate the behavior of a real battery system under specific conditions or scenarios. The goal is to predict how a battery will perform in real-world situations. Simulation uses the mathematical models developed through battery modeling to assess variables such as voltage, current, temperature, and state of charge (SoC) over time. Battery simulation is often done in the latter stages of product development to enhance designs, optimize control algorithms, and determine the performance of a battery system in a virtual environment before physical prototypes are built.
How EV batteries have evolved:
Over the years, there have been continuous improvements with EV batteries in terms of their energy density, charging speed, cost, and overall performance. Early EVs, such as those in the late 19th and early 20th centuries, used lead-acid batteries. Though simple and inexpensive, they were excessively heavy and had poor energy density. In the early to mid-20th century, nickel-iron batteries emerged, delivering better cycle life compared to lead-acid batteries. However, they also had lower energy density and were eventually replaced by other technologies, such as nickel-cadmium (NiCd) batteries (mid-20th century), which had better energy density and longer cycle life. In the late 20th century, nickel-metal hydride batteries emerged and they delivered much better energy density and eliminated the use of toxic cadmium. They were widely used in the first generation of mass-produced electric and hybrid vehicles. In the late 20th century, lithium-ion batteries revolutionized the EV industry due to their higher energy density, lighter weight, and longer cycle life.
Continuous R&D in lithium-ion battery technology has led to improvements in electrode materials, electrolyte formulations, and overall battery chemistry. These advances have resulted in higher energy density, longer range, and improved safety. That said, lithium-ion batteries are not particularly environment-friendly as they are made with rare-earth metals that are expensive to extract—and are often controlled by countries with problematic governments. For these reasons, the pursuit of new battery technologies and materials that are sustainable, safer, cost-effective, and better performing is ongoing.
Today, solid-state batteries are a next-generation technology being researched for EVs. These batteries replace the liquid electrolyte with a solid electrolyte, offering potential advantages in terms of safety, energy density, number of materials, and durability. Researchers are also exploring advanced lithium-ion chemistries and post-lithium technologies, such as lithium-sulfur and lithium-air batteries. These technologies are being pursued to further improve energy density and alleviate concerns about shortages of materials used in current lithium-ion batteries. Battery designers are now seeking unconventional ways to develop next-generation batteries—and are extensively using modeling software and battery simulators to realize their goals.
Key challenges in EV battery R&D—and how battery simulators help to meet them:
There are a host of economic and environmental pressures driving innovation to meet key challenges in EV battery R&D, including:
Improving energy density: Increasing energy density has always been a primary battery R&D challenge—and remains so today. Higher energy density extends range and makes battery packs more compact. Without longer ranges EV drivers will continue to experience range anxiety, a key constraint in EV adoption.
Battery simulators are useful tools for calculating EV range by incorporating detailed mathematical models that represent the electrochemical characteristics of batteries. These models consider parameters such as voltage, current, SoC and temperature. Different types of batteries have different performance characteristics, and the simulator integrates the specific characteristics of the battery used in the EV.
Battery simulators are often combined with vehicle simulation models that replicate real-world driving conditions and incorporate speed, acceleration, deceleration, road gradient and other variables. The simulator takes into account the power demand from the electric motor, considering factors like aerodynamics, rolling resistance, and drivetrain efficiency.
Simulators use predefined or customizable driving cycles that represent typical driving scenarios, such as city driving, highway driving or a combination of both. The simulator calculates the energy consumption of the EV under different driving conditions by simulating the battery’s discharge and recharge cycles. They also consider factors such as regenerative braking, which recovers energy during deceleration.
Some simulators allow users to input specific parameters, such as the desired speed, driving habits, payload, and external conditions like temperature and wind speed. External factors, such as climate control usage, can be included in the simulation to provide a more accurate estimate of the energy consumption under real-world conditions.
The simulator continuously calculates the SoC of the battery during a simulated drive. This dynamic SoC calculation is essential for estimating the remaining energy in the battery at any given point.
Improving battery charging: The charging of EV batteries is a complex process that must factor in battery characteristics, charging infrastructure, thermal management, grid integration, the user experience, and adherence to standards.
During the charging process, EVs sustain energy losses, beginning with the conversion of AC grid power to DC battery power. This conversion involves transformers, rectifiers, and other components that generate energy loss. When EVs are charged at higher voltages to decrease charging time, there are also higher energy losses. Furthermore, some energy is lost as heat during charging through resistance in the battery and chemical reactions in the cells. On top of this, charging at extreme temperatures can result in additional losses.
Battery simulation is a powerful tool for improving EV battery charging and minimizing energy losses by:
- optimizing charging algorithms;
- managing thermal behavior;
- analyzing fast charging scenarios;
- optimizing SoC management;
- assessing battery degradation;
- adjusting voltage and current profiles;
- enabling smart charging strategies;
- enhancing the user experience, and
- ensuring compliance with standards.
Reducing cost: The cost of manufacturing batteries remains a significant barrier to the mass adoption of EVs. Researchers are working on developing more cost-effective materials, manufacturing processes, and exploring economies of scale to bring down the overall cost of EV batteries.
Continued research into new and advanced materials is essential for developing new generation batteries. However, based on the entire periodic table of elements, there are trillions of potential material combinations that could be explored to determine combinations leading to the development of EV batteries that are safer, renewable, and more powerful, durable and cost-effective. The only realistic way to explore these combinations, from both a time and cost perspective, is through virtual prototyping with battery modeling and simulation.
Extending battery life and durability: The longevity of batteries and their ability to maintain performance over time are critical factors. Researchers are focused on improving the cycle life of batteries, minimizing capacity fade, and developing strategies for extending the overall lifespan of EV batteries.
Simulators model the degradation mechanisms of batteries over charge-discharge cycles. This information can be used to predict the lifespan of a battery under different usage scenarios and develop strategies to extend cycle life. Simulators also allow for virtual stress testing, where batteries can be subjected to extreme conditions without damage. This helps researchers understand failure modes and design more durable batteries.
Thermal management: Managing heat generated during charging and discharging is crucial for battery safety and performance. Researchers are developing advanced thermal management systems to increase the efficiency and safety of EV batteries, especially during fast charging and high-performance scenarios.
Battery simulators model heat generation during charging and discharging processes. This is crucial for understanding thermal behavior and developing effective thermal management systems to prevent overheating and improve overall efficiency.
Meeting automotive test standards: The automotive industry has established test standards to ensure the safety, performance, and reliability of EV batteries. Battery simulators play a crucial role in helping EV battery manufacturers meet these standards by providing a virtual environment for testing, analysis, and optimization. For example, simulators are used to test different thermal management strategies under a range of operating conditions. They also facilitate accelerated aging studies by simulating charge and discharge cycles;
helping optimize the long-term performance of batteries to meet or exceed lifecycle expectations. In addition, simulators can simulate failure modes, such as thermal runaway or short circuits, to assess the impact on battery safety. What’s more, battery simulators help researchers analyze and optimize fast-charging protocols. The role of battery simulators to help manufacturers meet automotive test standards is extensive, and contributes greatly to the development of reliable, safe, and high-performance EV batteries.
REGATRON battery simulators:
G5.BAS series
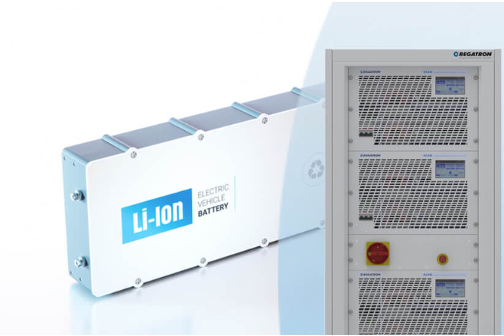
REGATRON has applied its many years of field experience and knowledge gained from ongoing work with renowned end users to develop the new G5.BAS battery simulator series. Suitable for use in laboratories and on test benches, the series realistically and dynamically simulates both the electrochemical and electrical properties of a battery type in charge and discharge mode. Other features include very high resolution of charge/discharge voltage and current, high system dynamics, and options for meeting high safety standards for operators.
The DC power supplies of the G5.BAS series are bidirectionally regenerative. Features such as adjustable controller settings and the integrated powerful 8-channel digital scope help the user quickly and easily achieve optimal system behavior for a specific application. The G5.BAS series also offers the possibility to store, edit and recall any device configuration on board the power supply.
TC.GSS series
The TC.GSS series is a full bidirectional series of high-power DC source / sink units based on field-proven REGATRON grid-tied technology. The wideband AC input module accepts nearly all AC grid systems worldwide and disposes of an active Power Factor Correction. The novel bidirectional converter architecture allows for very fast and continuous “quadrant crossing” between source and sink operation and vice versa, so a full current source to full current sink action takes only 2-3 milliseconds under ohmic load.
G5.BatSim
PC-software for battery simulation
REGATRON’s user-friendly battery simulation software G5.BatSim is designed for simulation battery modules and packs with charge and discharge capabilities of a few kW up to the 2000+ kW range. In conjunction with the powerful real-time computing process of a G5 device, even steep changes in charge/discharge currents can be handled with the required dynamics and stability.
REGATRON battery simulators from TMetrix:
TMetrix offers a full range of REGATRON battery simulators for EV battery R&D. Click here to start a conversation with one of our experts in the field.